Production of raw plastics creates a sooty residue that’s costly to clean. Now, the University of Wisconsin-Milwaukee is involved in promising research on a new material that could dramatically reduce both soot formation and associated costs.
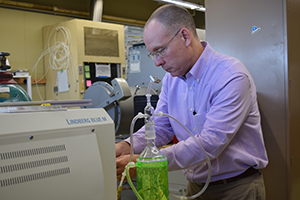
In April, Benjamin Church, associate professor in materials science and engineering, received a three-year U.S. Department of Energy grant for $239,111 to test a newly patented alumina-forming alloy that could be used to save millions of dollars in the manufacturing of hydrocarbons, namely ethylene.
According to the National Institute of Standards and Technology, ethylene — the building block of plastic — is the most widely produced organic compound in the world. It is manufactured by refining crude oil.
In the ethylene manufacturing process, carbon builds up inside reactor tubes, which degrades efficiency, Church said. To clean the tubes, furnaces must be shut down periodically. The downtime costs a plant upwards of $1 million a day in lost productivity.
Working with MetalTek International in Waukesha, Church will test the new alloy’s ability to dramatically resist carbon buildup, referred to as “coking,” during the ethylene manufacturing process. MetalTek is a leading manufacturer of centrifugally cast heat resistant tubes used in a variety of petrochemical processing applications including ethylene production.
“The goal is to improve a manufacturing process for core materials that our industrial world relies on,” Church said. “Our specific goal is to dramatically slow carbon buildup, perhaps by 90 percent. Our hope is that this new alloy will prove to be more energy efficient and most cost effective.”
A team at Oak Ridge National Laboratory in Tennessee, led by Govindarajan Muralidharan, has patented the alloy and received a $3.9 million grant from U.S. Department of Energy to commercialize it, Church said. The team turned to industrial and academic partners — UWM and MetalTek in Wisconsin, Duraloy Technologies in Scottsdale, Penn., and ArcelorMittal, in East Chicago, Ind. — to test and manufacture the material.